Coated Aluminium Foil Tape: The Ultimate Guide
Coated aluminium foil tape is a type of adhesive tape that is commonly used in various industries. It is made of a thin layer of aluminum foil coated with a layer of adhesive on one or both sides. The adhesive used can vary depending on the application, but it is typically a strong and durable acrylic adhesive.
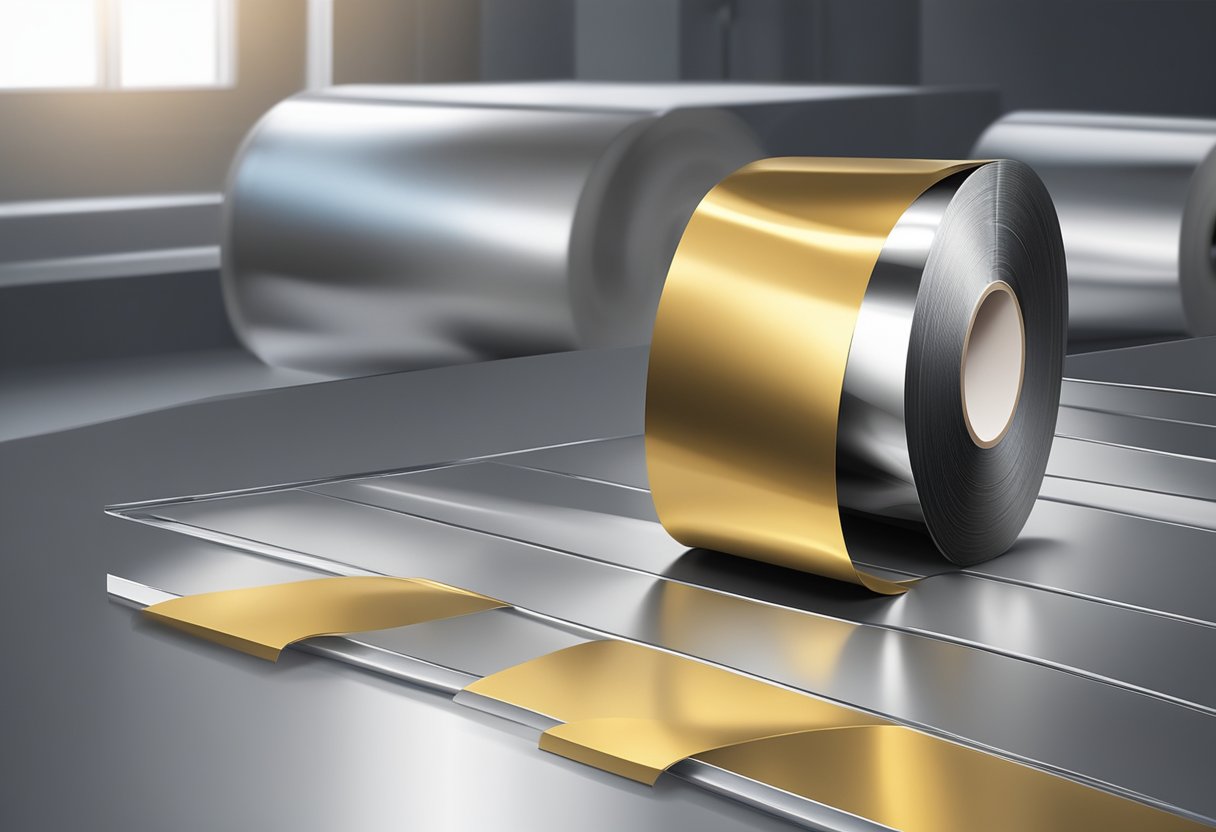
One of the key advantages of coated aluminium foil tape is its versatility. It can be used in a wide range of applications, from sealing ductwork and insulation to mounting and bonding materials. Additionally, the tape is highly resistant to moisture, chemicals, and extreme temperatures, making it ideal for use in harsh environments.
Product Overview
Coated aluminium foil tape is a type of adhesive tape that is commonly used in various industries for its excellent heat and moisture resistance properties. This tape is made by applying a layer of adhesive to one side of an aluminium foil and then coating it with a protective layer.
Composition and Properties
The primary component of coated aluminium foil tape is aluminium, which is known for its excellent thermal conductivity, corrosion resistance, and strength. The adhesive used in this tape is typically a synthetic rubber or acrylic-based adhesive, which provides excellent adhesion to a wide range of surfaces.
The protective layer on the top of the tape is usually made of a polymer material, such as polyethylene or polypropylene, which provides additional protection against moisture, chemicals, and UV radiation. Coated aluminium foil tape is available in different thicknesses, ranging from 0.18mm to 0.25mm, and can withstand temperatures up to 150°C.
Manufacturing Process
The manufacturing process of coated aluminium foil tape involves several steps. First, the aluminium foil is cleaned and treated to remove any impurities or contaminants. Then, a layer of adhesive is applied to one side of the foil using a coating machine.
After the adhesive is applied, the foil is coated with a protective layer to prevent it from getting damaged during transportation and storage. The protective layer can be either a release liner or a polymer film, depending on the application.
Finally, the coated aluminium foil tape is cut into rolls of various sizes and packaged for distribution. The manufacturing process ensures that the tape is of high quality and meets the required standards for different applications.
In conclusion, coated aluminium foil tape is a versatile and reliable adhesive tape that is widely used in various industries. Its excellent properties and manufacturing process make it a preferred choice for many applications that require heat and moisture resistance.
Applications
Coated aluminium foil tape is a versatile product that has many applications in various industries. Here are some of the most common applications:
Industrial Usage
Coated aluminium foil tape is widely used in the industrial sector for sealing and insulation purposes. It is often used to seal ductwork, pipes, and other mechanical systems. The tape’s high-strength adhesive ensures a secure bond, even in high-temperature environments. It is also resistant to moisture, chemicals, and UV radiation, cloth tape making it ideal for use in harsh industrial environments.
Electrical Insulation
Coated aluminium foil tape is an excellent electrical insulator. It is often used to wrap electrical wires and cables to protect them from moisture, heat, and other environmental factors. The tape’s high dielectric strength ensures that it can withstand high voltages without breaking down, making it ideal for use in electrical applications.
HVAC Industry
Coated aluminium foil tape is widely used in the HVAC industry for sealing and insulation purposes. It is often used to seal air ducts and pipes to prevent air leaks and improve energy efficiency. The tape’s high-strength adhesive ensures a secure bond, even in high-temperature environments. It is also resistant to moisture, chemicals, and UV radiation, making it ideal for use in HVAC applications.
In conclusion, coated aluminium foil tape is a versatile product that has many applications in various industries. Its high-strength adhesive, resistance to moisture, chemicals, and UV radiation, and excellent electrical insulation properties make it an ideal choice for sealing and insulation purposes.
Advantages
Durability
Coated aluminium foil tape is known for its durability and strength. The aluminium foil backing provides exceptional resistance to tearing and punctures, making it ideal for use in harsh environments. The tape’s adhesive is also highly durable, ensuring that it remains securely in place even under extreme conditions.
Thermal Resistance
One of the key advantages of coated aluminium foil tape is its excellent thermal resistance. The tape can withstand high temperatures without losing its adhesive properties or degrading in quality. This makes it an ideal choice for applications where heat resistance is critical, such as HVAC systems, insulation, and electrical wiring.
Moisture Barrier
Coated aluminium foil tape is also an excellent moisture barrier. The tape’s backing is impermeable to water and other liquids, making it ideal for use in damp or humid environments. Additionally, the tape’s adhesive is highly resistant to moisture, ensuring that it remains securely in place even in wet conditions.
Overall, coated aluminium foil tape is a versatile and reliable solution for a wide range of applications. Its durability, thermal resistance, and moisture barrier properties make it an ideal choice for use in harsh environments where other tapes may fail.
Installation Guidelines
Before installing the coated aluminum foil tape, it is important to properly clean and prepare the surface. Any loose debris or dirt should be removed to ensure good adhesion.
The tape should be applied to a dry surface at temperatures between 10°C and 40°C. If the temperature is below 10°C, it is recommended to warm the surface and the tape before application.
When applying the tape, it is important to use firm pressure to ensure good adhesion. It is recommended to use a roller or a similar tool to ensure the tape is properly bonded to the surface.
In order to achieve the best results, it is recommended to apply the tape in a continuous strip, avoiding any gaps or overlaps. If necessary, the tape can be easily cut with scissors or a knife to fit the desired length.
Overall, following these installation guidelines will ensure that the coated aluminum foil tape is properly applied and provides a strong and durable bond.
Performance Characteristics
Adhesion Quality
Coated aluminium foil tape offers excellent adhesion quality due to its pressure-sensitive adhesive coating. This adhesive layer is designed to bond strongly to a variety of surfaces, including metal, plastic, and glass. The tape’s adhesion quality ensures that it remains in place, even in harsh environments or when exposed to extreme temperatures.
Temperature Range
Coated aluminium foil tape is designed to withstand a wide range of temperatures, making it suitable for use in a variety of applications. The tape can withstand temperatures ranging from -30°C to 150°C, making it ideal for use in both hot and cold environments.
In addition, coated aluminium foil tape is resistant to moisture, chemicals, and UV radiation, making it suitable for use in outdoor applications. It is also highly durable and can withstand wear and tear, making it an ideal choice for industrial and commercial applications.
Overall, coated aluminium foil tape is a versatile and reliable solution for a wide range of applications. Its excellent adhesion quality, temperature range, and durability make it an ideal choice for a variety of industries, including construction, automotive, and aerospace.
Standards and Certifications
Coated aluminium foil tapes are widely used in various industries due to their exceptional properties. To ensure the quality and safety of these tapes, several standards and certifications have been established.
One of the most recognized standards in the industry is the UL 723 standard. This standard measures the surface burning characteristics of building materials and is used to determine the fire resistance of coated aluminium foil tapes. Tapes that meet the UL 723 standard are considered to be safe and reliable for use in buildings.
Another important certification for coated aluminium foil tapes is the ASTM International certification. ASTM International is a globally recognized organization that develops and publishes technical standards for various materials, products, and systems. The ASTM certification ensures that the tape meets the required quality and performance standards.
In addition to these standards and certifications, some manufacturers also provide their own certifications and test reports to ensure the quality of their products. These certifications and reports can provide additional information on the tape’s performance and suitability for specific applications.
Overall, it is important to choose coated aluminium foil tapes that meet the required standards and certifications to ensure their quality and safety.
Safety and Handling
When handling coated aluminum foil tape, it is important to take certain precautions to ensure safety. The following guidelines should be followed:
- Always wear appropriate personal protective equipment (PPE) when handling the tape, such as gloves and safety glasses.
- Avoid contact with skin and eyes, as the tape adhesive can cause irritation or allergic reactions.
- Store the tape in a cool, dry place away from direct sunlight and heat sources to prevent degradation of the adhesive.
- Do not expose the tape to chemicals or solvents, as this can damage the adhesive and affect its performance.
- Use caution when cutting the tape, as the edges can be sharp and cause injury.
- Dispose of used tape properly according to local regulations.
By following these safety guidelines, users can minimize the risk of injury and ensure the tape performs as intended.
Environmental Impact
Coated aluminium foil tape has a relatively low environmental impact compared to other materials commonly used in construction and manufacturing. The tape is often made from recycled aluminium and can be recycled again after use, reducing the amount of waste sent to landfills.
The adhesive used in coated aluminium foil tape is typically a solvent-based acrylic adhesive, which has a lower environmental impact than solvent-based rubber adhesives. However, some manufacturers have begun to use water-based acrylic adhesives, which have an even lower environmental impact.
In terms of energy use, the production of coated aluminium foil tape requires less energy than other materials such as steel and copper. This is due to the lightweight nature of aluminium and the fact that it can be easily formed into thin sheets.
Overall, coated aluminium foil tape can be considered a relatively environmentally friendly option for a variety of applications. However, it is important for manufacturers and users to properly dispose of the tape after use and to consider alternative options such as reusable materials when possible.
Market Trends
Coated aluminium foil tape has been gaining significant traction in recent years due to its versatility and durability. The market for coated aluminium foil tape is expected to grow steadily in the coming years, with a CAGR of 5.2% from 2021 to 2028.
One of the key drivers of this growth is the increasing demand for coated aluminium foil tape in the construction industry. The tape is widely used for sealing, bonding, and repairing HVAC ducts, pipes, and other construction materials. The growing construction activities in emerging economies are expected to drive the demand for coated aluminium foil tape in the near future.
Another factor contributing to the growth of the market is the increasing use of coated aluminium foil tape in the automotive industry. The tape is used for heat shielding, vibration damping, and electrical insulation in automobiles. With the growing demand for electric vehicles and the increasing focus on reducing emissions, the demand for coated aluminium foil tape in the automotive industry is expected to increase significantly.
Moreover, the rising demand for coated aluminium foil tape in the packaging industry is also expected to drive the market growth. The tape is widely used for packaging and sealing of food and pharmaceutical products due to its excellent barrier properties and resistance to moisture, heat, and chemicals.
Overall, the market for coated aluminium foil tape is expected to witness steady growth in the coming years, driven by the increasing demand from the construction, automotive, and packaging industries.
Future Developments
As technology continues to advance, the future of coated aluminium foil tape looks bright. Manufacturers are constantly researching and developing new ways to improve the performance and durability of the tape.
One area of focus is enhancing the adhesive properties of the tape. This could involve the development of new adhesives or the modification of existing ones to improve their bonding strength and longevity.
Another area of potential development is the use of thinner foil materials. This could lead to improved flexibility and easier application of the tape in tight spaces.
Manufacturers may also explore the use of new coatings or laminates to improve the tape’s resistance to extreme temperatures, moisture, and other environmental factors.
Overall, the future of coated aluminium foil tape looks promising, with continued advancements in technology and materials leading to improved performance and versatility.